SPECIAL APPLICATION PUGMILLS
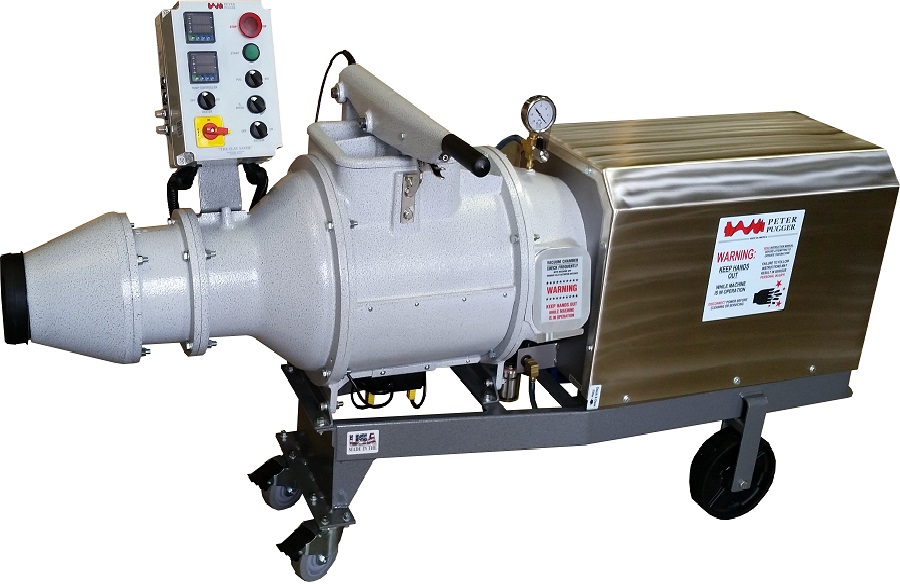
VPM-60MCE
MIX + DEAIR + HEAT + EXTRUDE = SAVINGS
“THE ULTIMATE PUGMILL”
Comes equipped with 240V electrical for standard service.
PRICE BASED ON OPTIONS
Click here to learn how automotive manufacturing companies save money using a Peter Pugger
The Clay Saver combines the capability of batch mixing polymer, epoxy and carbon based materials with the convenience of a pugmill output. All scrap goes right back into the hopper and is recycled, vacuum deaired, heated, and pugged. Currently used in the following industries:
-AUTOMOTIVE
-AEROSPACE
-CARBON BATTERY
-MICROCHIP
-SATELLITE
-ARTS & CRAFTS
The VPM-60MCE has been able to replace the need for multiple pieces of equipment to process or reclaim various materials.
Aggressive Stainless Steel Auger: The auger design has been modified to accommodate the enormous back pressure generated as a result of extruding large amounts of clay through a small orifice (tile die/adapter).
Stainless Steel: Shaft, augers and paddles of stainless steel, along with an aluminum mixing/pugging chamber ensures rust-free clay processing.
High Quality, Heavy Duty Drive: The industrial rated electric motor, close coupled to a gear reduction transmission, is the highest quality gear drive system available. Overload protection is provided in the magnetic motor starter.
Large Hopper: The oversized hopper door allows for easy loading of up to 140 lbs. of clay per batch (based on standard hopper door operation. Large hopper hood allows for continuous feeding of material.
Batch Mixing Capability: Full batch mixing and blending capability allows for thorough mixing and temperature adjustment before extruding.
Pugmill Output: Switch to PUG after a batch is completely mixed, and the Power Wedger unloads itself in the form of various output configurations.
Vacuum Deaired: Each batch can be deaired by starting the vacuum pump during the last stage of mixing, leaving an air-free product when pugged out (no need to run the clay through the pugmill multiple times). Once the entire batch of clay has been deaired, switch the pugmill to PUG, and press start. Any remaining deaired clay in the machine can be stored for later use without having to remix or deair. Our patented vacuum design allows us to deair the entire batch of clay without the use of cumbersome vacuum/shredding screens, or down time due to a clogged pugmill! No other mixing pugmill on the market matches the Peter Pugger’s effectiveness at deairing clay. We guarantee it!
Sealed Chamber: Here in our Northern California Factory, each pugmill casting has precision CNC machined o-ring grooves incorporated into them which allows the pugmill to effectively store moist clay indefinitely! No other pugmill on the market provides this level of precision when it comes to properly sealing all pugmill surfaces.
Intellectual Mixing Technology: Real-time monitoring of clay consistency can be accomplished while mixing. Similar to an automatic transmission, the Pugger-Mixer can automatically speed up or slow down based on the hardness of the clay being processed. The operator can also control the speed by controlling the variable speed knob.
Patented Vacuum Chamber: The Patented Vacuum Chamber serves as a separation chamber between the processing chamber (where clay is mixed and pugged) and the gear drive system. In the event the pugmill is overfilled, the excess clay is collected in the vacuum chamber where it can be easily accessed and redirected back into the processing chamber in time for the next batch (if necesary). The Vacuum Chamber door is designed to disengage before excess clay can generate enough pressure to damage the gear drive system. This is a key design feature for mixing pugmills where clay is being forced up against the rear of the processing chamber during the mixing cycle. Peter Pugger is the only mixing pugmill to provide extra protection against vacuum and bearing seal exposure resulting in maintenance free operation (US Patent No. 5261638, 4322169, & 5716130).
Upgraded Motor: In addition to the massive gear reduction the gearbox provides, an upgraded 5Hp motor has been designed into the VPM-60MCE to provide ample power.
Tile Nozzle: The VPM-30TE has the ability to utilize the standard nozzle with a 3″ diameter pug or a tile nozzle with a 10″ wide x 2″ tall opening. Nozzles can be switched out by simply removing the four bolts that secures the nozzle to the cone.
Variable Speed Control: This allows the operator the ability to speed up or slow down the pugmill. This is especially useful when extruding through dies. Because of the back pressure generated by a large amount of clay being forced through a small orifice, the speed control allows the operator to slow the pugging as required. In turn, perfect deaired configurations are easily extruded through the Pugger-Mixer. There are additional advantages if you are a “single potter studio”. The ability to slow the pugging allows for time to place pugged clay into containers or bags.
On Wheels: The VPM-60MCE comes with 8″ diameter wheels. It is easily transported for cleaning and storage.
Work Surface: The motor and drive are enclosed for protection, cleanliness and safety. A stainless steel cleanable work surface is provided on top for convenience of the operator while loading.
Temperature Controlled Chambers: Materials can be stored indefinitely inside the machine. The barrel and nozzle chambers are temperature controlled to maintain warm material. The temperature controls for the nozzle and barrel chambers are factory set to the specific materials being recycled to provide consistent results. Minimum temperature settings have been incorporated into the controls to provide protection against cold batch starts. In turn, the machine will begin reclaiming only when the temperature has reached the minimum temperature requirement.
Real Time Readout: The VPM-60MCE comes equipped with an amperage gauge which provides real-time readout of mixing activity. As the material is being mixed, the amperage gauge will provide the amps being pulled based on the motor demand. Once the gauge reaches the desired amp level, the material is ready for the deairing and extruding process.
The VPM-60MCE Controller With Nozzle and Barrel Heater Controls
The VPM-60MCE is the most versatile processing machine on the market today. It can perform a variety of functions efficiently, transforming clay in any form to a usable product. Some examples:
- Mix moist clay from powder and water.
- Reclaim scrap – wet or dry.
- Blend two or more different bodies.
- Add materials (wet or dry) to an already moist body.
- Adjust moisture of an already wet body.
- OR just mix a 25 lb. bag of clay – literally warm the clay by mixing it.
When the clay is adequately mixed, it can be deaired with vacuum and pugged out in the form of logs ready for use.
It is not necessary to continuously hand-feed the Power Wedger as with standard pugmills. Load a full batch, close the lid and turn it on – this eliminates exposure to moving paddles. The Power Wedger shuts off automatically when the lid is opened. All machines are equipped with a thermal overload for protection against overheating.
Vacuum is provided by a 1/2 HP double-headed rocking piston type diaphragm pump. These new technology pumps are the simplest and quietest vacuum source available. They are maintenance-free and long lasting. The VPM-60MCE Power Wedger does not require a large vacuum pump because the clay is continuously exposed to vacuum in the sealed mixing chamber. Once the clay chamber is evacuated, the vacuum pump can be turned off.
The VPM-60MCE comes with 8″ wheels so it can be easily moved to a cleaning site. With the removal of eight bolts, the entire nozzle and cone section can be removed so it can be conveniently washed off. The paddles are then easily accessed for cleaning. Cleaning is necessary only to avoid cross contamination. Since the machines are completely sealed, moist clay can be stored indefinitely without drying out.
- Variable Speed Control: Yes
- Extrusion Dies (See Accessories): Optional
- Standard 3.5″ Diameter Nozzle: Yes
- Tile Nozzle & Adapter Plates: Optional
- Pug Cutter (See Accessories): Optional
- Safety Lock Out: Optional
- Vacuum System: Yes
- 208-240 Electrical Availability: Yes
- 3 Phase Electrical Availability: Optional
- 60HZ Electrical Availability: Yes
- 50HZ Electrical Availability: Optional
- Large Feeding Hopper: Optional
- Auto Cutting System: Optional
Large Feeding Hopper (Optional)
Automatic Cutting System (Optional)
Specifications
- Maximum Batch Capacity: 85-100 pounds (Depends on Material)
- Pugging Rate: 1,500+ lbs. per hour
- Mixing Time: 4-6 minutes
- Heating System: Dual Temp Control-Barrel/Nozzle
- Dimensions: 65″L x 24″W x 31″H
- Crated Weight: Aluminum Version – 640 lbs. (Ships LTL Trucking)
- Hopper Door Size: 9″ x 9″
- Pug Size: 3.5″ round (standard)
- Electrical: 5 HP 1-phase, 24 amps at 240V
- Vacuum Pump: 1/2 HP, 3 amps at 240 volts, 30A Plug