VPM-9HC High Compression Pugmill
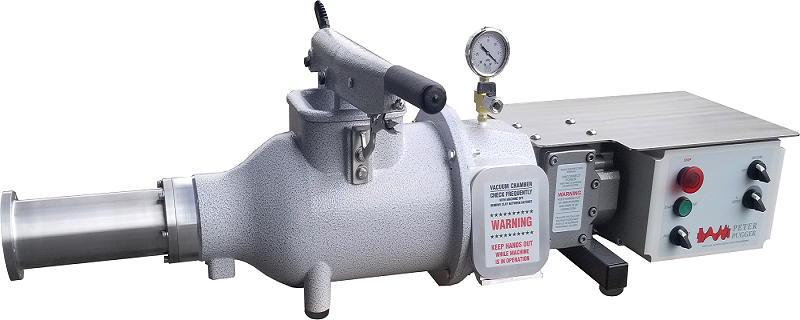
VPM-9HC High Compression Pugmill
(25 lb. Max. Batch Size)
“The Vacuum Deairing Pugger-Mixer”
Comes equipped with 110V electrical for standard service.
220V operation ($100 additional) also available for overseas operation.
$7,549
The VPM-9HC utilizes all the latest advancements in mixing, deairing and extruding technology. The development of a high compression zone and 3D adapter for mounting canisters lands the VPM-9HC High Compression Pugmill in a class of its own.
Additive manufacturing, also known as 3D Printing, is an automated process used to create rapid prototypes and functional end-use parts. It takes virtual designs from computer-aided design (CAD) software and transforms them into thin, virtual, horizontal layer-wise cross-sections until the model is complete. Multiple applications of 3D Printing across various end-user industries, such as ceramics, automotive, aerospace, defense, healthcare, construction, and architecture continue to advance. Metals, plastics, and ceramics are some of the media being used in conjunction with 3D Printing.
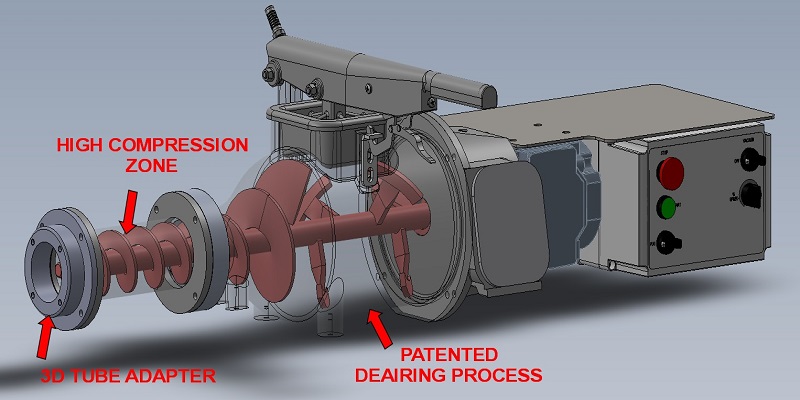
High Compression Auger and Extension Spool: The VPM-9HC comes equipped with an aggressive high compression auger that generates the needed pressure for filling 3D canisters. Because the high compression auger is longer than the standard VPM-9 auger, an extension spool has been provided to house the high compression auger and allows for 3D adapters (sold separately) to be mounted to the end.
Batch Sizes: The VPM-9HC, which mixes up to a maximum of 25 Ibs. of moist clay. (Capacities vary depending on clay condition, type, moisture, etc).
Stainless Steel: Shaft, augers and paddles of stainless steel, ensures corrosion-resistant clay processing.
Aluminum: Mixing/Pugging Chamber made from 356A Aluminum Alloy.
Large Hopper: The oversized hopper door allows for easy loading of up to 25 lbs. of clay per batch.
Batch Mixing Capability: Full batch mixing and blending capability allows for moisture adjustment before pugging.
Pugmill Output: Switch to PUG after a batch is completely mixed to begin moving material through the high compression zone and 3D adapter. (3D canisters and adapters not included).
Vacuum Deaired: Each batch can be deaired by starting the vacuum pump during the last stage of mixing, leaving an air-free product when pugged out (no need to run the clay through the pugmill multiple times). Once the entire batch of clay has been deaired, switch the pugmill to PUG, and press start. Any remaining deaired clay in the machine can be stored for later use without having to remix or deair. Our patented vacuum design (Click here for full list of patents) allows us to deair the entire batch of clay without the use of cumbersome vacuum/shredding screens, or down time due to a clogged pugmill! No other mixing pugmill on the market matches the Peter Pugger’s effectiveness at deairing clay. We guarantee it!
Sealed Chamber: Here in our Northern California Factory, each pugmill casting has precision CNC machined o-ring grooves incorporated into them which allows the pugmill to effectively store moist clay indefinitely! No other pugmill on the market provides this level of precision when it comes to properly sealing all pugmill surfaces.
Intellectual Mixing Technology: Real-time monitoring of clay consistency can be accomplished while mixing. Similar to an automatic transmission, the Pugger-Mixer can automatically speed up or slow down based on the hardness of the clay being processed. The operator can also control the speed by controlling the variable speed knob.
Patented Vacuum Chamber: The Patented Vacuum Chamber serves as a separation chamber between the processing chamber (where clay is mixed and pugged) and the gear drive system. In the event the pugmill is overfilled, the excess clay is collected in the vacuum chamber where it can be easily accessed and redirected back into the processing chamber in time for the next batch (if necesary). The Vacuum Chamber door is designed to disengage before excess clay can generate enough pressure to damage the gear drive system. This is a key design feature for mixing pugmills where clay is being forced up against the rear of the processing chamber during the mixing cycle. Peter Pugger is the only mixing pugmill to provide extra protection against vacuum and bearing seal exposure resulting in maintenance free operation (Click here for full list of patents).
Variable Speed Control: This allows the operator the ability to speed up or slow down the pugmill. This is especially useful when extruding through dies. Because of the back pressure generated by a large amount of clay being forced through a small orifice, the speed control allows the operator to slow the pugging as required. In turn, perfect deaired configurations are easily extruded through the Pugger-Mixer. There are additional advantages if you are a “single potter studio”. The ability to slow the pugging allows for time to place pugged clay into containers or bags.
Stainless Work Surface: The stainless steel work surface creates a durable work surface for convenience of the operator while loading.
Corrosion Resistant: Peter Pugger now offers a corrosion resistant high compression model (VPM-9HCSS) for potters using porcelain and white (based) clay bodies.
Optional Stand: This heavy duty stand has a shelf, and the height is adjustable. Wheels are included and can be installed on the motor end of the VPM-9 stand for easy transport (see picture below).
- Mix moist clay from powder and water.
- Reclaim scrap – wet or dry.
- Blend two or more different bodies.
- Add materials (wet or dry) to an already moist body.
- Adjust moisture of an already wet body.
- OR just mix a 25 lb. bag of clay – literally warm the clay by mixing it.
- Generates required pressure for high compression applications.
When the clay is adequately mixed, it can be deaired with vacuum and pugged into 3D canisters.
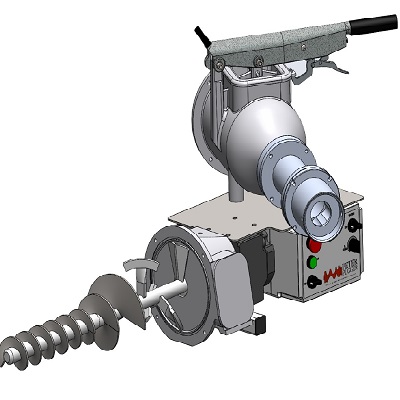
- Variable Speed Control: Yes
- Adjustable Stand (See Accessories): Optional
- Extrusion Dies (See Accessories): Optional
- Tile Nozzle Compatible: N/A
- Pug Cutter (See Accessories): Optional
- Safety Lock Out: Optional
- Vacuum System: (Included; runs off main electrical)
- 120V Electrical Availability: Yes
- 208-240 Electrical Availability: Optional
- 3 Phase Electrical Availability: N/A
- 60HZ Electrical Availability: Yes
- 50HZ Electrical Availability: Optional
Specifications
- Maximum Batch Capacity*: 25 pounds
- Pugging Rate: 500 lbs. per hour
- Mixing Rate: 150 lbs. per hour
- Dimensions: 50″L x 14″W x 14″H
- Crated Weight: Aluminum Version – 155lbs Ships Freight
- Hopper Door Size: 5.25″ x 5.25″
- Pug Size: 3″ round
- Electrical: 3/4 HP 1-phase, 8 amps at 120 volts, 6 amps at 240V
- Vacuum Pump: 1/2 HP, (operates off main electrical)
*Max Batch Capacity may vary depending on material density and moisture content